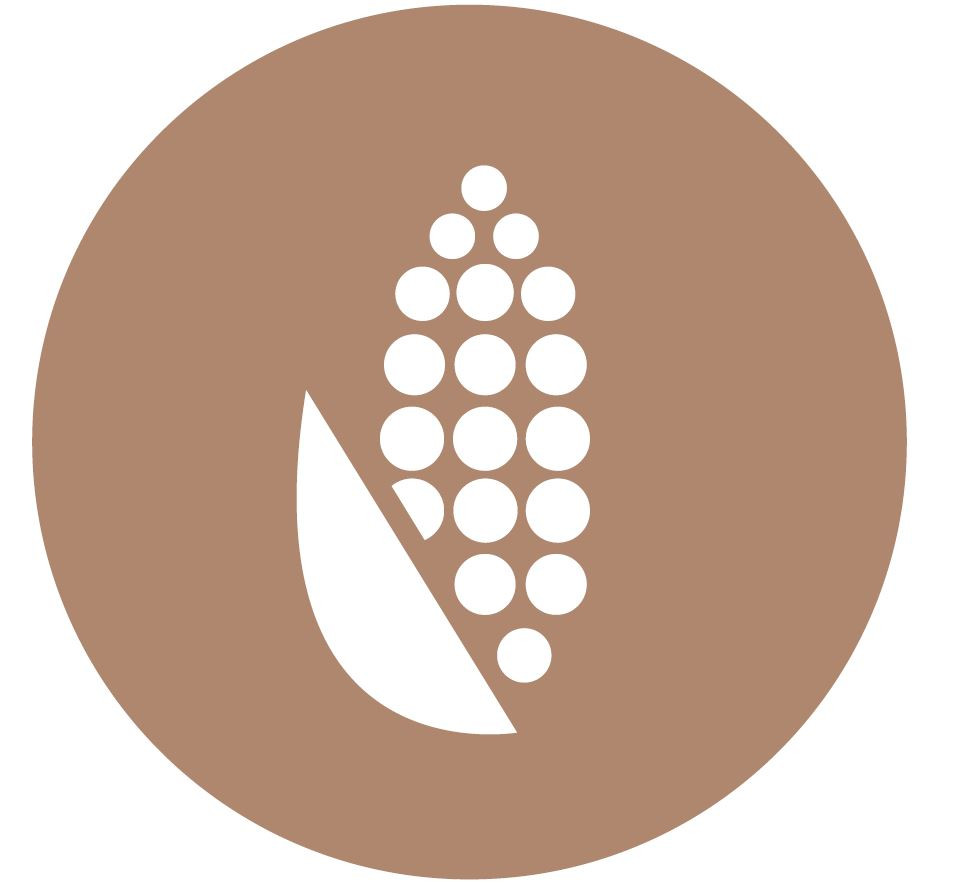
What is PLA Bioplastic?
14th Aug 2020
Polylactic acid (PLA): the environmentally responsible plastic.
What is PLA Bioplastic?
PLA can be made from plants such as corn. Polylactic acid or polylactide (PLA) is a polyester derived from renewable biomass, typically from fermented plant starch, such as corn, cassava, sugarcane, or sugar beet pulp.
How is PLA Produced?
Polylactic acid comes from bacterial fermentation of carbohydrates. PLA is a polyester (polymer containing the ester group) made with two possible monomers or building blocks: lactic acid, and lactide. Lactic acid can be produced by the bacterial fermentation of a carbohydrate source under controlled conditions. In the industrial scale production of lactic acid, the carbohydrate source of choice can be corn starch, cassava roots, or sugarcane, making the process sustainable and renewable. Research is ongoing to come up with even more eco-friendly and cheaper methods of producing PLA. In addition the agricultural produce itself – crop residue such as stems, straw, husks, and leaves – can be processed and used as alternative carbohydrate sources. Residue that cannot be fermented can be used as a heat source to lessen the use of fossil fuel-derived hydrocarbons.
Environmental Advantages of PLA
Composting is an ideal end-of-life option for PLA plastics. PLA is biodegradable under commercial composting conditions and will breakdown within twelve weeks, making it a more environmentally choice when it comes to plastics in contrast to traditional plastics which could take centuries to decompose and end up creating microplastics. The manufacturing process for PLA is also more environmentally friendly than that of traditional plastics made from finite fossil resources. According to research, the carbon emissions associated with PLA production are 80% lower than that of traditional plastic. PLA can be recycled as it can be broken down to its original monomer by a thermal depolymerization process or by hydrolysis. The outcome is a monomer solution that can be purified and used for subsequent PLA production without any loss of quality. However, the recycling infrastructure for PLA hasn’t been scaled up yet, mainly because end markets for the recycled material haven’t been developed. While recycling PLA might be a viable solution in the future, we currently recommend composting as a preferred end-of-life option, especially as foodservice packaging is often contaminated with food scraps, making recycling impractical.
Disadvantages of PLA
Monoculture crops can cause environmental problems for the land and water. Despite the numerous advantages of PLA, there are some disadvantages. Growing crops and using fertiliser have an impact on land and water, such as fertiliser run off and reduced soil quality (even though, in 2019, bioplastics represented 0.016% of total land use and are only expected to increase to 0.021% in 2024). PLA plastic packaging can be more expensive than conventional plastics, due to the number of steps required during production. However, as PLA becomes more widely available, efficiencies of scale will come into play, which means the cost will decrease.
PLA: A Circular Option
By switching to plant-based bioplastic, we can contribute to a circular economy which takes better care of our earth. The production of bioplastic has little to no effect on food prices or supply. In 2018 the global production capacities for bioplastics amounted to around 2.1 million tonnes. This translates into approximately 790,000 hectares of land. The surface area required to grow sufficient feedstock for today’s bioplastic production is therefore about 0.01% of the global agricultural area of 5 billion hectares. This ratio correlates with the size of an average cherry tomato next to the Eiffel Tower. In 2023, assuming continued high growth in the bioplastics market, at the current stage of technological development, a market of around 2.6 million tonnes accounting for about 975,000 hectares of land could be achieved. This market equates to approximately 0.016% of the global agricultural area. In fact, leading PLA manufacturer, Natureworks, has announced that 100% of its feedstock will be third-party certified sustainable feedstock by 2020. NatureWorks was the first biopolymers manufacturer to become certified to the new ISCC PLUS standard in 2012, and currently has more than 40% of its agricultural feedstock certified. At full capacity, more than 90 farms will be involved in the program by 2020. Every farm entering the program receives training in adhering to the ISCC PLUS certification’s principles, which are the following:
- Protect highly biodiverse and high carbon stock areas.
- Implement best agricultural practices for the use of fertilizers and pesticides, irrigation, tillage, soil management, and the protection of the surrounding environment.
- Promote safe working conditions.
- Comply with human, labour, and land rights.
- Comply with laws and international treaties.
- Implement good management practices and continuous improvement.
Natureworks is also committed to feedstock diversification, and to using the most abundant, locally available, and sustainable source of biobased carbon, wherever they produce. They are also committed to critically assessing and assuring the sustainability of each and every feedstock they use. Natureworks is now developing new PLA technologies: sugars from bagasse, wood chips, or straw, as well as assessing technology that could convert carbon dioxide or methane to lactic acid.
Information taken from BioPak's website. Read about our composting service, and the problem with labelling a product 'biodegradable', on our blog.
Planet Friendly Packaging acknowledges the traditional custodians of the land on which we work. Our thoughts go out to everyone affected by COVID-19. Stay safe.